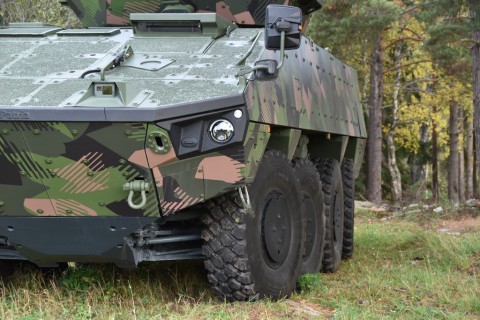
12.7.2016
The model for continuous improvement adopted by Patria’s Halli helicopter unit is known as HIP7. Based on close collaborative development with the customer, the model sought to identify novel approaches and a new culture, encouraging Patria to succeed together with the customer. The work began in May 2015, and the results speak volumes.
Text: Kaisa Mäki-Kullas
Photos: Kaisa Mäki-Kullas
The Halli unit’s proven expertise in helicopters dates back a long time in final assembly, retrofit modifications as well as maintenance. However, despite Patria’s experience and indisputable expertise, collaboration with the customer has not always been without complications.
Jerome Jaussaud from Airbus Helicopters is responsible for the company’s External Final Assembly Lines operations, and has worked with Patria since 2001.
“We were not quite happy with the situation. There were tensions in our collaboration, with Patria not always being able to keep its schedules,” comments Jaussaud. According to General Manager Harri Majanmaa, the unit itself saw that the trouble that Airbus had with material deliveries was the principal cause of the problems. This had a negative effect on the work flow, efficiency and job satisfaction.
Jerome Jaussaud, Airbus Helicopters, and Harri Majanmaa, Patria
Shared goals
Instead of engaging in mutual accusations, Patria and Airbus committed themselves to correcting the situation. Both parties sought to establish a genuine partnership instead of a traditional subcontracting relationship. Their sights were set on clarifying the division of responsibilities, resolving problems related to material deliveries, and developing Patria’s internal processes. The completion of this work was assigned to five development workgroups, the associated keywords being transparency, trust and responsibility. End-user satisfaction was given the highest priority.
In the practical work, Lean methods were applied both to shared and Patria’s internal and development processes. Airbus already has ten years’ experience of applying Lean methods, and Patria has used them for the past two years.
Information, enthusiasm and ideas
As nothing new is ever created in a vacuum, Patria embarked on investing in Lean training, energetically seeking experiences and insights from outside the company, for example, by conducting a fact-finding trip to Airbus’ factory in Donauwörth, Germany. “Although we carry out modifications and repairs instead of manufacturing new products, we nevertheless gained a large number of new ideas and concrete tips, of which the flow of materials from storage directly to technician and the models for solving technical problems with helicopters deserve a mention,” comments Jukka Korja, technicians team leader. In addition to training and study trips, Patria also sought assistance from external experts. Through the Airbus connection, an experienced Lean consult who had been in charge of the production of NH90 helicopters at the time it began in the Airbus German factory was engaged in the process. A Finnish expert introduced Patria to value stream analysis. Visual management techniques are an important part of the daily work. Work follow-up visualised on boards clarifies and illustrates the current work situation. At present, each working day at every machine begins with a brief five-to-ten minute meeting at the boards. The measurement of progress, quality and efficiency, and prompt reacting on any deviations is particularity important.
Technicians team leaders Jukka Korja and Matias Rantala have also familiarised themselves with Lean methods while completing their special vocational qualifications.
From problems to success
One of the central issues to emerge from the model is reporting on problems. General Manager Majanmaa emphasises problem handling and the aspect that problems in the daily work are either solved on site or escalated without delay to the next level in order to find a quick solution.
“Things will get moving immediately after a problem is reported, and nowadays you can count on the fact that a solution will soon be found,” says Matias Rantala, technician team leader, confirming Majanmaa’s report.
The project has resulted in many success stories. For example, the time required by the dismantling and preparing for delivery of components known as NORIA parts – part of the early phase of a retrofit project – has been shortened from two weeks to two days. Previously, a dozen articulated lorries were required for transports; today, a single vehicle will take the components to the Airbus plant in France.
The new operating models have also been adopted by the final inspection function, through which helicopters pass before being transferred to flight readiness in anticipation of a test flight. The number of remarks concerning repairs has almost halved, and the number of hours spent on repair work has decreased by approximately 40 percent.
“We have made significant progress, making work flow smoother. If work can be carried out without interruptions or having to take steps backward, which has a positive effect on work motivation,” comments Majanmaa, satisfied. “We want to be a reliable and flexible partner, one that always puts a premium on the customer.”
Continuous improvements at the core
“The development project has required a great deal of work, but now we have common goals in place and a view on things that we can share. An atmosphere of trust, transparency and flexibility has been taken to a new level,” says Jerome Jaussaud from Airbus Helicopters.
The management of materials that has caused divergent views has been brought under control. The recognition of bottlenecks, new and shared process descriptions, material descriptions and schedules have all contributed to the work and made it flow considerably more smoothly. Patria sent one employee to Airbus in France for a period of six months with the purpose of identifying problems, creating personal networks and finding new approaches in collaboration with Airbus.
“Now that we have shared and standardised KPIs for measuring our operations, we are in a position to concentrate all our energy on the result. We expect and we believe that the experiences and benefits brought about by the HIP7 development project will also show in a positive way in our future collaboration with our Swedish customer,” says Jaussaud.
“Continuous improvement is now in everybody’s DNA here!”
Patria’s Helicopter unit at Halli has around 120 employees. The unit assembles NH90 helicopters and performs maintenance and structural modifications on them. Between 2003 and 2015, the unit assembled 29 NH90 helicopters. The Airbus Helicopters retrofit-programme on the 15 NH90 transport helicopters of the Finnish Defence Forces began in Halli in 2014, continuing until 2018, and seven helicopters of the Swedish Armed Forces will undergo the same programme between 2016 and 2020. The heavy maintenance of the NH90 squadron of the Finnish Defence Forces is also carried out in Halli.
HIP7 = Halli Improvement Plan – 7 helicopters a year
What did you like about the article?
Thank you for your opinion! You can share the article on social media using the buttons below: