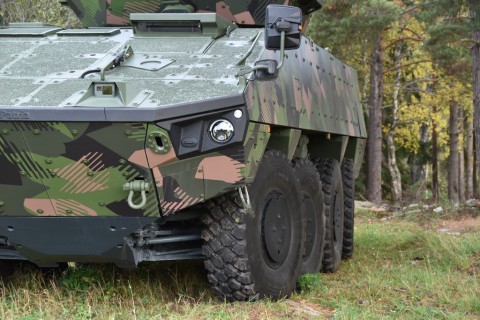
27.3.2023
Patria services the emergency diesel generators that keep nuclear power plants safe in the event of disruptions.
Nuclear power plants are playing an increasingly important role in European energy management – and their operational safety must be carefully maintained also in the future. Patria contributes to ensuring nuclear safety by maintaining the diesel engines that are used to generate electricity to power critical functions in the event of any disruptions.
“The emergency diesel generators start running if the nuclear power plant stops receiving electricity from the main grid. The generators ensure that the cooling systems of the nuclear power plant remain up and running even when a malfunction occurs, and the plant can be safely shut down if necessary,” says Anita Korsberg, Business Development Director at Patria.
Patria has serviced and repaired heavy-duty diesel engines for nuclear power plants since the early 1990’s at its Linnavuori plant in Nokia.
Patria services, in addition to Finnish nuclear power plants, also diesel generators for French nuclear power plants, and has a variety of customers around the world.
“We’re always on the lookout for new customers, especially among European nuclear power plants,” says Korsberg.
Basic overhaul every 15–20 years
A nuclear power plant generally has 3 to 4 emergency diesel generators per reactor. The plants are highly reliable and thus the engines accumulate few operating hours.
However, to ensure safety, the engines must be kept in working order and readiness at all times. Test runs are performed monthly to verify this.
The basic overhaul interval for reserve power systems varies from plant to plant. A complete overhaul is usually performed every 15–20 years.
“Just the ageing process of certain engine parts makes this necessary. These include rubber seals, for instance,” says Korsberg.
When a generator – which is about the size of a minibus – arrives at Linnavuori, it is completely dismantled and each part is cleaned and inspected. Wearing parts are automatically replaced.
After the overhaul, the engine is tested and then delivered back to the nuclear power plant. Between basic overhauls, Patria can also carry out major on-site maintenance tasks. However, the nuclear power company usually handles the annual maintenance of diesel generators on its own. This work includes changing lubricating oils and filters, for instance.
Maintenance is highly regulated
On average, Patria carries out basic overhauls on 2 to 5 emergency diesel generators per year. Maintenance work must adhere to strict safety regulations. It is always overseen by a supervisor, such as an independent classification society invited by the nuclear power company or the representative of an authority such as the Radiation and Nuclear Safety Authority of Finland.
In addition to quality standards, the work is steered by official guidelines issued by the authorities. All maintenance measures must also be carefully documented. “Documentation is a big part of this job. The fi nal report of a single engine maintenance operation runs to hundreds of pages, and in some cases to over a thousand,” Korsberg says.
Aleksi Ojala, Senior Vice President, Operations, says that strict quality requirements fi t well with Patria. The Linnavuori repair workshop is used to complying with stringent safety regulations – in addition to diesel engines, it also carries out strictly regulated maintenance of aircraft engines. “For instance, we’re very familiar with meticulous documentation,” says Ojala.
Over the years, Patria has invited its customers to meet and discuss the maintenance of nuclear power plant diesel generators and exchange best practices. “All parties benefit from sharing technical information and experiences. These engines must remain operational for decades. One of the essential considerations is to ensure the availability of spare parts,” says Korsberg.
The cooperation network is very useful when you have to find a certain spare part for a decades-old engine – it might be fastest to source that part from another nuclear power plant. New technologies are being introduced to make it easier to obtain spare parts. In the future, Patria may be able to manufacture some of the necessary components using additive manufacturing – that is, 3D printing.
Long experience is very useful
Ojala says that Patria’s long experience of high-quality work and strict compliance with regulations are absolute strengths of the engine repair workshop. Tailoring the maintenance work to the requirements of each customer and engine type also calls for expertise.
“In all that we do, quality is everything. We always complete our work in close cooperation with the customer. It’s also essential to come up with solutions that save costs for the customer,” Ojala says.
He says that long-term cooperative relationships are based on trust. For instance, when Patria recommends using a certain repair method, the customer can rest assured that it is the most cost-effective solution and has been carefully thought through.
“Customers also value flexibility. Maintenance work doesn’t always stick to the planned schedule, which means the repair workshop has to be adaptable,” says Ojala.
Patria’s engine repair workshop has its roots in the State Aircraft Factory, founded in 1921. It has operated in Linnavuori, Nokia since 1947.
The engine repair workshop services the gas turbine engines of aircraft and helicopters and it specialises in diesel engines for heavy industry, Army vehicles and Navy vessels. Anita Korsberg estimates that over the past years the Linnavuori diesel repair workshop has serviced equipment made by 30–40 different engine manufacturers. There are well over a hundred different engine versions. “This is interesting work, as the engines, their repair methods and means of producing spare parts are evolving all the time.”
What did you like about the article?
Thank you for your opinion! You can share the article on social media using the buttons below: