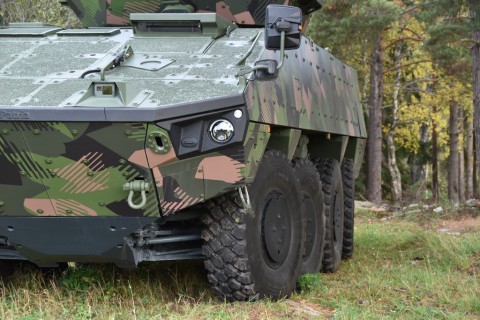
26.5.2014
The state of the art qualities of the new vehicle are the result of exhaustive product development. The requirements are transferred from paper to the prototype and are tested on the track until they have been fine-tuned to the last detail for the future needs of customers.
Text: Heini Santos and Patria
Photos: Matti Immonen
The morning of the test day dawns clear. The bright spring sun dissipates a couple of degrees of frost, softening the muddy surface of old airfield area at the Parolannummi garrison. Sami Oja, Chief Designer of the steering and suspension in Patria’s new vehicle, scans the testing area. Oja’s colleague, Test Engineer Juha Kauppinen, peers out from the armoured vehicle’s hatch and runs through the day’s plan. In addition to testing the suspension, the aim for the day is to clock up more kilometres for trials long-term durability. The preceding days have been spent working intensively in the office. New components and features, and often completely new solutions, have to be continuously tested in conjunction with product development. Within this context, the test engineer plans and prepares the tests in collaboration with the test mechanic. The actual test consists largely of routine repetition in accordance with a pre-prepared plan, followed by an examination and analysis of the results and the final reporting. On this occasion, components relating to the vehicle’s suspension will be tested. All the critical parameters will be measured and recorded for further analysis and inclusion in the actual test report. An essential part of the testing consists of reference measurements to prevent the effects of changes in conditions during the test, with a view to eliminate errors. At this point, the test seems to an outsider like a continuous and even exhaustive repetition of measurements over and over again. Two-way voice communication between the driver and the operator of the measuring equipment makes it possible to respond immediately if one or the other notices something unexpected. Kauppinen continually keeps Oja abreast of his observations, which help improving driver operating experience and ease of use.
"There are numerous things that are not necessarily apparent on the drawing board, but which emerge in practice. Our task is to put the finishing touches to the vehicle so that it will be ready for future projects and associated customer tests and, of course, for the vehicles’ end users,” Kauppinen says.
Off-road terrain performance
One of the main features of Patria’s new vehicle, which was unveiled at the DSEI 2013 event in London, is its improved payload efficiency, that is, a higher percentage of the total weight of the vehicle is payload capacity for the customer. The tests are conducted using a gross weight of 30 tonnes. In order to achieve this weight, tonnes of extra weightsare placed on the vehicle and attached to the sides to simulate the weapons systems to be installed in the customer versions, protection and personnel with equipment. The vehicle’s 13-tonne payload capacity has already been verified. The future growth potential of the vehicle is being determined by means of the current trials and measurements.
“One of the main objectives of the project, i.e. maintaining the vehicle’s off-road performance despite its increased combat weight, is the basis of everything. Patria AMV has been the undisputed winner in numerous customer trials, which is why it is used by seven different customers. Now we are making the best even better. Our new, ground-breaking solutions are working really well,” Oja says.
Tests are conducted using a gross weight of 30 tonnes; to achieve this weight, tonnes of iron is mounted on the sides and top of the vehicle. Efforts are made to maintain the vehicle's performance despite of the increased combat weight.
The toughest tests for the vehicle are off-road trials. Patria’s test team is very familiar with the most challenging locations in the off-road areas it uses. In line with the test plan, Kauppinen reverses the new vehicle up a narrow forest road in order to take a run up the steep and muddy hill. The vehicle forges to the top and then pushes through the narrow and steeply inclined track, accelerates on the bumpy straight and wades through various sized puddles and ponds in which blocks of ice are floating. In addition to the forest terrain typical of Finland, the vehicle is also tested on sand and in other conditions required by export markets. "This will definitely get through the most incredible places. Like Patria AMV, it is really hard to get this vehicle stuck. And should this nevertheless happen, the vehicle's winch will get it going again." In addition to events that are predictable and can be analysed, unexpected and surprising things can occur, especially in the most extreme tests. A component breakdown does not mean disaster; rather it is an indication of the need for further development, and hence leads to further improvement of the vehicle. The tests identify and verify the vehicle’s limits and, if necessary, solutions are sought which raise the bar even higher – we are making vehicles for the future needs of our customers, and that is when “good” is not enough.
“It’s great to go flat out”
It is essential for the test driver to stay calm, even in tough situations. On the other hand, he has to be a bit of a daredevil and sometimes ready to take risks. “The driver must be familiar with the vehicle so that he can test its limits without damaging the vehicle. He must also know how to read the terrain well so that he is able to select the right tracks in good time,” says Technical Manager Toni Töyrylä, who is in charge of vehicle product development. The team responsible for developing the new vehicle consists of a number of designers and two test drivers: Juha Kauppinen and Test Mechanic Tapio Hakari. Hakari’s catch phrase “It’s great to go flat out” indicates that practical testing is the spice of the test group’s work. “The preparations are often long compared to the measurements themselves. After weeks of advance preparations, there might be only one day of driving. The results are analysed and potential modifications are carried out before a new test, and then the same cycle is repeated,” Hakari says. A certain impulsiveness is needed when seeking the extreme limits. “The driver cannot be afraid of the vehicle getting stuck in the terrain, for example. Knowing the limits comes from experience, and from awareness that gradually you can go further and further. Even if everything is measured with precision, the driver himself must be able to assess what is happening and how the run feels,” he explains.
T-shirt or winter overalls?
New vehicle concept being tested on Hyvinkää airfield. The image shows full braking under maximum friction conditions.
Finland’s geographical location and testing laboratories enable trials to be conducted in extreme conditions. The toughest tests are perhaps heat and cold tests designed to ensure that the vehicle and its systems function in temperatures ranging from 46 degrees below zero to a sweltering 49 degrees. The figures are based on the climatic categories laid down in NATO’s standards, which cover the entire inhabited world. Individual customers may nonetheless require verification of functionality in even warmer temperatures.
“We have a high-temperature chamber where the properties of the vehicle can be tested at different temperatures and the systems are operated under load with the vehicle connected to a dynamometer. Air-flow during driving is simulated with huge fans that blow air at about 100 kilometres per hour. While the other test personnel follow the trial in the convenience of air-conditioned premises, heat tests mean a sweaty working day for the driver as, depending on the testing programme, the vehicle’s air conditioning might not be used during the tests. It is like sitting in a lukewarm sauna,” Kauppinen says. Over the years, testing in Finland has been supplemented by a number of tests carried out in real desert conditions and, as a result, Patria’s vehicles have been successfully fielded by a number of customers around the world in extremely hot conditions. Outdoor winter tests measures factors relating to usability, such as heating, insulation and startup of the vehicle in cold temperatures. Cold tests are also conducted during the summer – in a low-temperature chamber. “Northern conditions raise the standard for cold conditions so high that not all customers will ever need all of the vehicle’s low-temperature features. In the far north, we make vehicles that run in both cold and hot climates – temperatures in the environment where the vehicle is used can vary by more than 100 degrees,” Oja says.
New features for future customer needs
Patria AMV is today’s most successful modern 8x8 armoured wheeled vehicle. Delivery contracts to Sweden and South Africa provide the most recent evidence of this. Patria is developing its product portfolio continuously, and along with this new vehicle significant new features have emerged which are aimed for future customer needs. Significantly higher payload, unrivalled off- and on road mobility, optional amphibious capability, increased electrical power output, user friendly use of space and ergonomics and numerous minor improvements make this new vehicle superior solution for its future users. Its well-thought modular vehicle architecture and build in growth potential enable its use in various operational roles. Patria will be participating in future procurement projects with vehicle solutions tailored to meet the requirements of each project – always in accordance with customer requirements. This article was published in the Patria magazine in June 2014.
What did you like about the article?
Thank you for your opinion! You can share the article on social media using the buttons below: