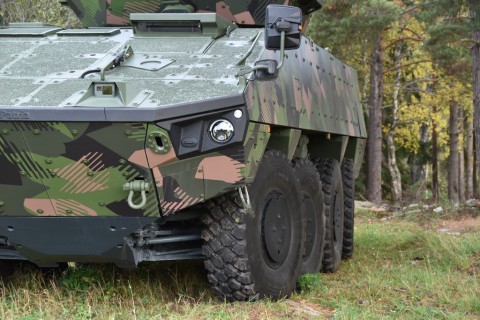
Patria's Engineering capabilities cover a wide variety of services from damage and repair analysis to design of preventive modifications and structural health monitoring programmes.
The use of modern analysis software tools guarantees our airframe structural repair design capability whether it comes to fatigue or accidental damage. Our structural Finite Element Models are based on a complete airframe simulation loaded with integrated pressure distributions. Combined with accurate submodels, they are effective tools for managing structural issues.
Engineering
- Design work for aircraft mechanical and electrical major modifications and repairs
- Modeling and analysis (FEA) of aircraft structures and components: stress/strength, stability, eigen frequency, transient dynamics
- Fatigue and fracture mechanical analysis: crack initiation and growth, critical crack length.
- Strength, vibration and fatigue testing of aircraft structures and performance testing of mechanical components/devices
- Flight parameter based structural fatigue monitoring system with neural networks (NN), providing full fleet/flight coverage for pre-selected locations
- Aircraft mechanical systems modeling, co-simulations with partners (VTT, TAU) and analysis (MBD)
- Aerodynamical (CFD) and flight mechanics modeling and analysis
- Data analytics and development of analysis methods and tools with a/c maintenance and flight record data (big data):
- aircraft design and usage spectra comparisons (Nz, altitude, weight… ), search for and compilation of statistics on occurrence of specific flight conditions.
- structural fatigue monitoring with individual a/c usage, fatigue life estimation with typical usage spectra
- Used methods: Finite Element Analysis (FEA), Multi-Body Dynamics (MBD), Computational Fluid Dynamics (CFD), Advanced data-analytics together with big data, reverse engineering, 3D-scanning, additive manufacturing.
- Softwares: CATIA V5/V6, Enovia PDM-software, MSC.Patran, MSC.Nastran, MSC.Adams, FINFLO, Matlab, Simulink, S1000D
Systems engineering and technical support
- Aircraft mechanical and avionic systems expertise
- NDT Level 3 in MPI, FPI, PT, ET, UT, MT and RT methods. ST and RT Level 3 during 2020.
- Magnetic particle inspection (MPI)
- Fluid penetrant inspection (FPI)
- Radiographic inspections (RI)
- Ultrasonic inspections (UI)
- Eddy current inspections (EC)
- Laser shearography (LS)
- Welding repairs and multiple thermal spraying repairs and surface treatment
- Continuous maintenance development activities together with customer.
- Creating and maintain working processes and maintenance service manuals
Technical Publications group
- Producing complex technical documentation using XML-based publishing systems
- FrameMaker and Xyvision Professional Publisher (XPP) for Boeing F/A-18 Hornet and BAE Hawk manuals
- International S1000D specification to produce an IETP/IETM solution for Hawk maintenance documentation on a content lifecycle management (CLM) platform.